Pet coke is a low molecular carbonaceous solid product of thermal cracking of the residual oil from the vacuum distillation column in oil refineries. In India, the cement industry is the largest end-user segment of pet coke. It is able to use high volumes of pet coke as its high sulfur content is neutralised by limestone in clinkerisation process.
The demand for pet coke from the cement industry is estimated to grow at a rate of 24 per cent. An average petroleum refinery may produce as much as 2,000-5,000 tonnes of pet coke every day. Also, coke mixed with coal makes it more economical than pure coal, which makes this industry more interesting for the power sector.
Tenova TAKRAF (India) Pvt. Ltd, being a leader in dry cargo handling, is well equipped with the required technical knowledge and decades of experience to design and supply systems for this thriving industry.
The 9.02-million tpa Guru Govind Singh Refinery Project of HPCL-Mittal Energy Ltd at Bathinda, Punjab, is one of the major recent installations by TAKRAF India. HEML has two DCUs which produce coke at a rate of 3,150 tpd each. This amount is continuously sent to their destinations through rail loading system and/or truck loading systems. To avoid disruption of work in times of no production of coke, a stock of about 10 days worth of pet coke (around 42,000 tonnes) is kept in storage.
Conveyor belts (nylon) are used to transfer the coke from one point to another. The belts are made oil resistant and are designed to handle the incoming coke at 50o temperature. These were designed for 500 tph capacity, with rated capacity of 450 tph. Walkways are provided on both sides of the conveyor belt for maintenance purposes, and are covered with handrail pipe constructions (middle, top, knee guard and toe guard) for safety purposes.
Stockpiling and reclaiming of materials is carried out by the 500-tph stacker-cum-bucket wheel reclaimer. This is equipped with a travelling arrangement, on rail tracks. The stacking boom (luffing and slewable type) is kept as close as possible to the pile top to prevent dust generation. The PLC on the machine is pre-programmed to carry out the stacking procedure. This can also be operated and monitored from a remote location like the central control room, using wireless radio wave technology. Payloaders are kept for assistance, which may also be used for reclaiming in emergency situations. Conveyors then transfer the reclaimed pet coke from the stockpile to either the silo of the RLS or the truck loading bunkers.
Rail loading system
The rail loading system is located in a straight portion of the railway tracks, which receives the pet coke from stockpiles and DCUs. The concrete silos are provided with suitable liner, inspection doors and inspection platforms, complete with all accessories and other loading equipment like load cell mounted weigh hopper, hydraulically operated gate and hydraulic loading chute. The wagon loading is done through flood loading system and is controlled from control room located on the first floor of the silo. The overall rate of loading is 3,600 tph, matching the variation of creep speed of locomotive. This is achieved by means of a load cell mounted weigh hopper and hydraulically operated loading spout. The level of material inside the silo is continuously assessed by a monitoring device which gives audio-visual signal as soon as it reaches the pre-set value. The level indication devices are located outside the silos with suitable enclosure for maintenance. All equipment is electrically and mechanically interlocked to ensure starting and stopping of their drives in a sequence or as required for logical operation of the system. Adequate time lag is provided to avoid overloading of the electric/hydraulic system.
The truck loading bunkers comprise a structural steel building having three loading bunkers for loading onto tippable trucks. All loading bunkers are provided with ultrasonic level indicators at the top which continuously indicate the material levels inside the bunkers based on which the feeding system starts/stops. The bunker mouth is provided with electrically operated sector gates with suitable telescopic chute mechanism for loading onto the trucks.
The online belt weigher is made complete in all respects with speed sensor, hermetically sealed and temperature compensated load cell etc. It is provided with auto correction facility to set right any deviation from actual rate of conveying over the pre-set/rated capacity. Road weighing stations are set up near the truck loading bunkers to monitor the weights of the outgoing trucks. Similar in-motion railway bridges are installed after the second silo to monitor the weights of the loaded wagons.
Water-based dust sprinkler systems are used to reduce the emission of dust. Pump stations are set up to cater water supply to all the sprinklers and are designed to cater for at least 25-30 minutes in case of shortage of water supply. In addition to the dust suppression system, cooling systems for power packs and fire-fighting systems are also installed for emergency situations.
Tenova TAKRAF, located in Chennai, belongs to Tenova Mining & Minerals division and is represented in all major countries. In the last five years, over 200 machines and systems have been supplied by the company for a variety of stockyard operations to major cement manufacturers, power producers and mining companies in India and other parts of the world, especially in the Middle East and Africa.
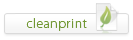
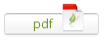
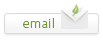